Patricia J. Reis and Stefanie Wuschitz joined forces with Kristin Weißenberger to learn about sustainable and low-energy consumption ceramics, for creating tiles as PCBs and other speculative electronic components. Stefanie wanted to explore gold alternatives like Pyrit and gain skills in making clay boards. Patricia wanted to experiment with burning conductive materials in the same process as burning the ceramics, to be able to process the complete PCB made from ubiquitous materials and with low energy consumption by ourselves and on-site. To accomplish this we joined a workshop by artist and stone age expert Heinz Lackinger (https://www.heinzlackinger.at/). He taught us how to identify soil and specific earth in the ground, particularly in Burgenland, in the rural South East of Vienna, and create ceramics with them without using tools. This site contains prehistoric archaeological exacerbations by Romans, Celtics and older settlements who used the clay you can still find in this region, at the foot of Leitha mountains. Heinz discovered in decades of research how people in the stone ages created objects from adobe, loam, and loess only by adding water and exposing them to different temperatures in a wood fire. No tools, equipment or electricity was required, only adobe, water, fire and your fingers for shaping the mud. Having said that it could be defined as a technology, that uses all senses to select, prepare, manufacture and produce these objects. The smell, colour, humidity, temperature and shape as well as the age and consistency of clay play a significant role in identifying appropriate material. Heinz shared his expert knowledge on how to go about forming the objects and what materials shape the design, colour and general outcome of the final burned objects. To add dry cowpat to the fire add black colour to the ceramics. Coloured and black clay otherwise usually turns red when dry and stoved. Heinz explained the delicate balance of adding oxygen to the fire at the right moment or telling apart different temperature zones in the fire to avoid explosions in the clay. The two-day workshop was a meditative and sensuously enriching retreat that left us with two milestone insights. First, we can in fact create tiles that substitute common PCBs by using no or low-energy resources from ubiquitous materials. Second that we can stove conductive materials simultaneously with the clay to process circuits and make the connections durable. This helped us to move forward with proposing a consistent new artistic method of hardware production.
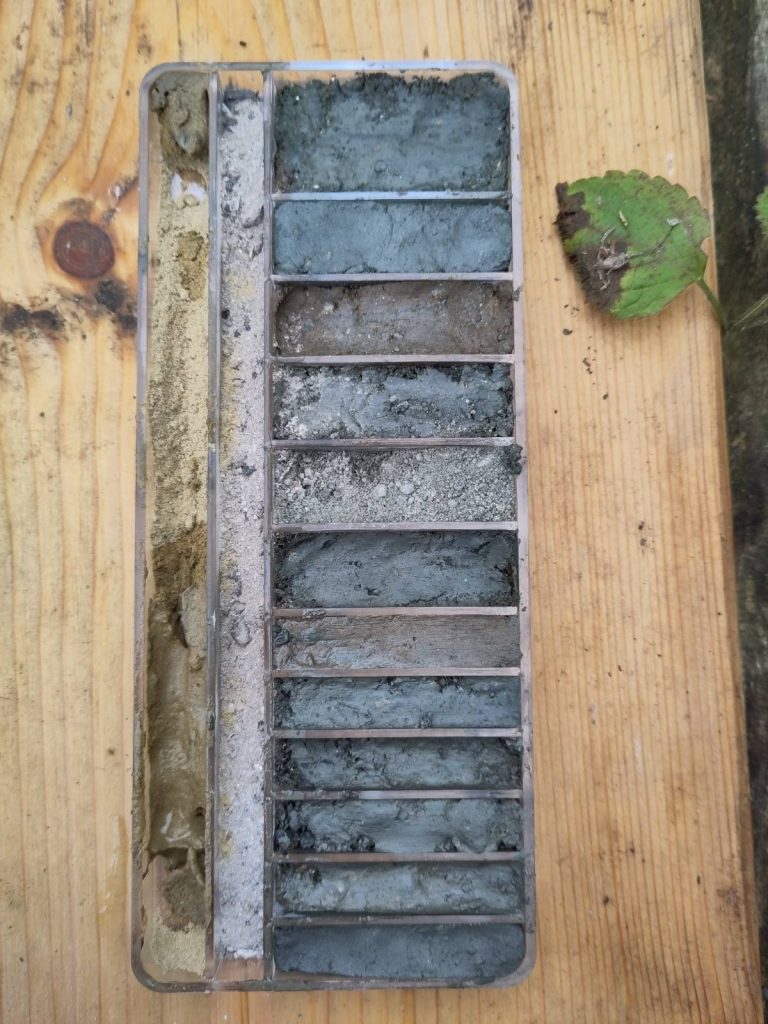
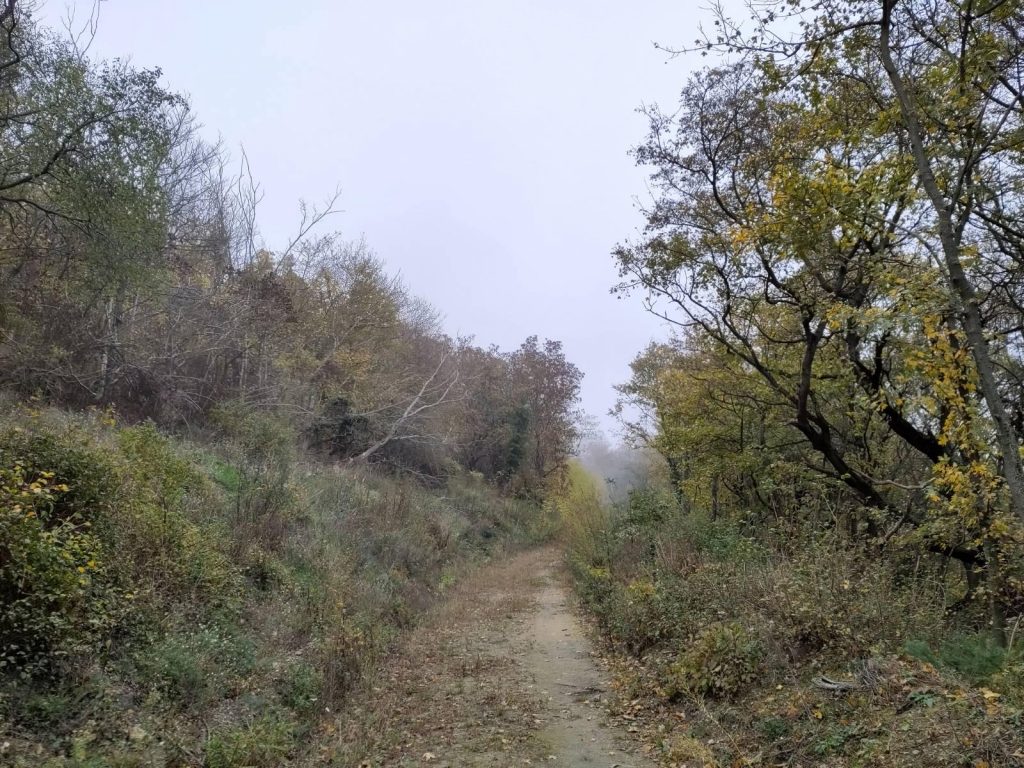
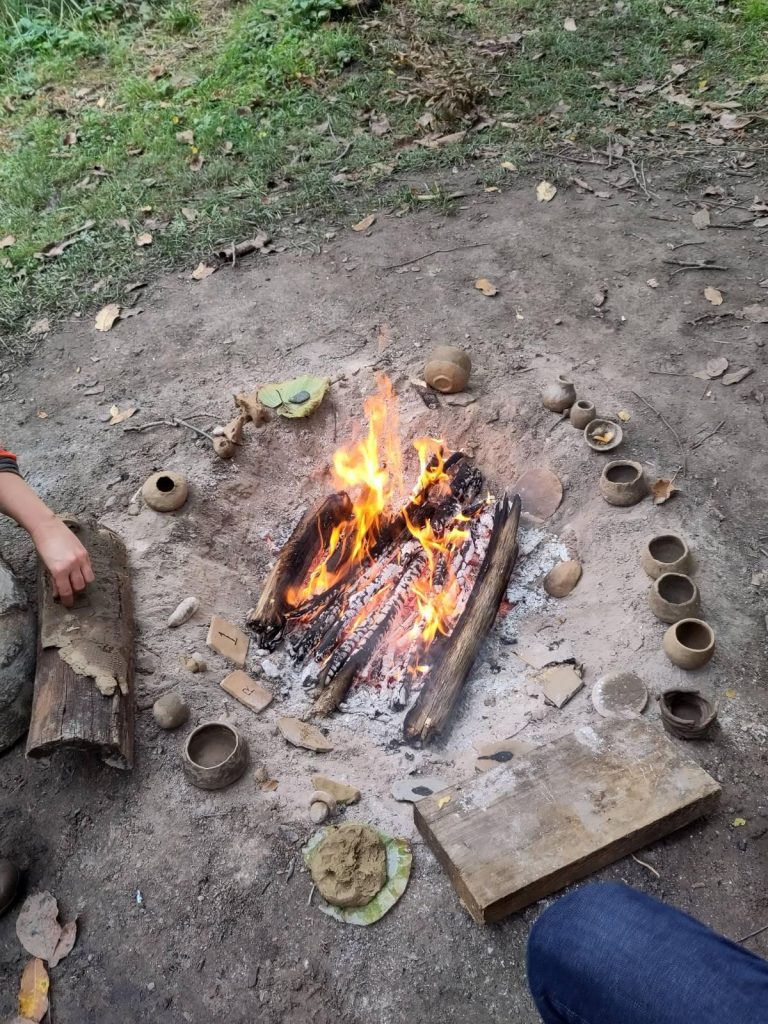
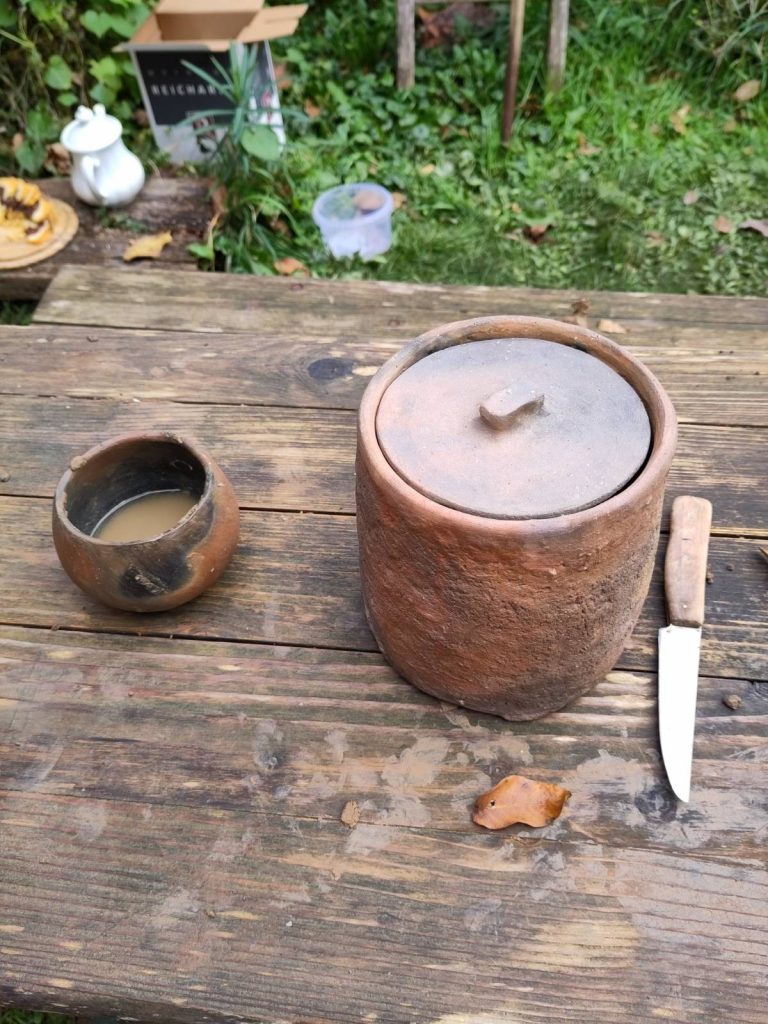
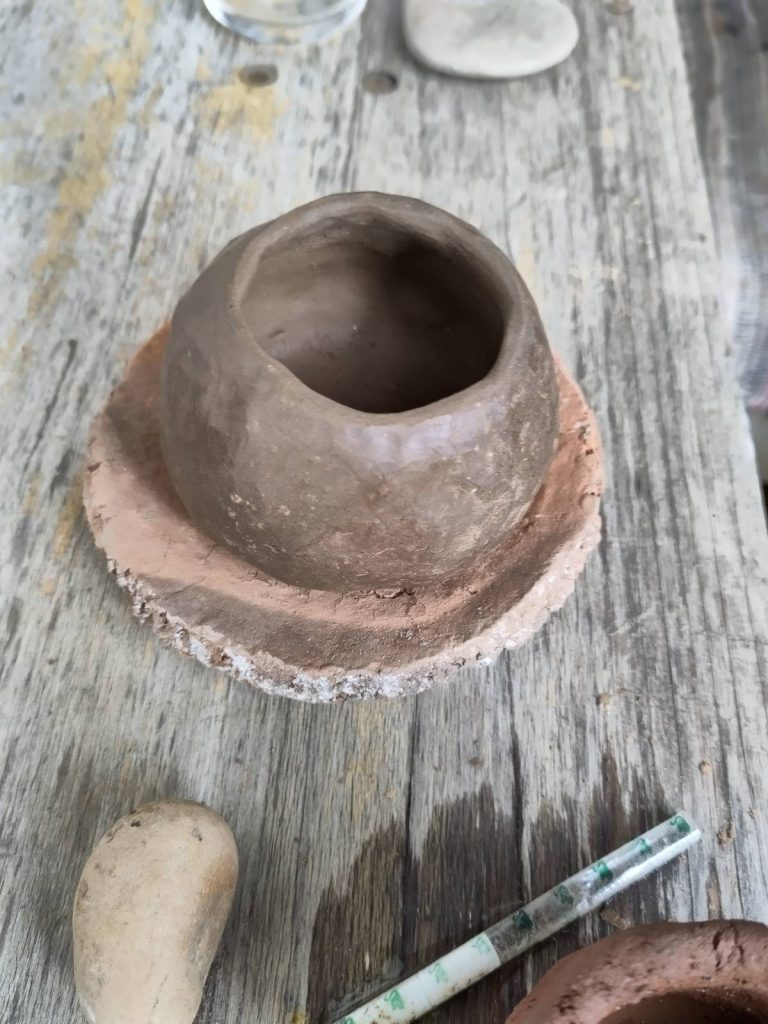
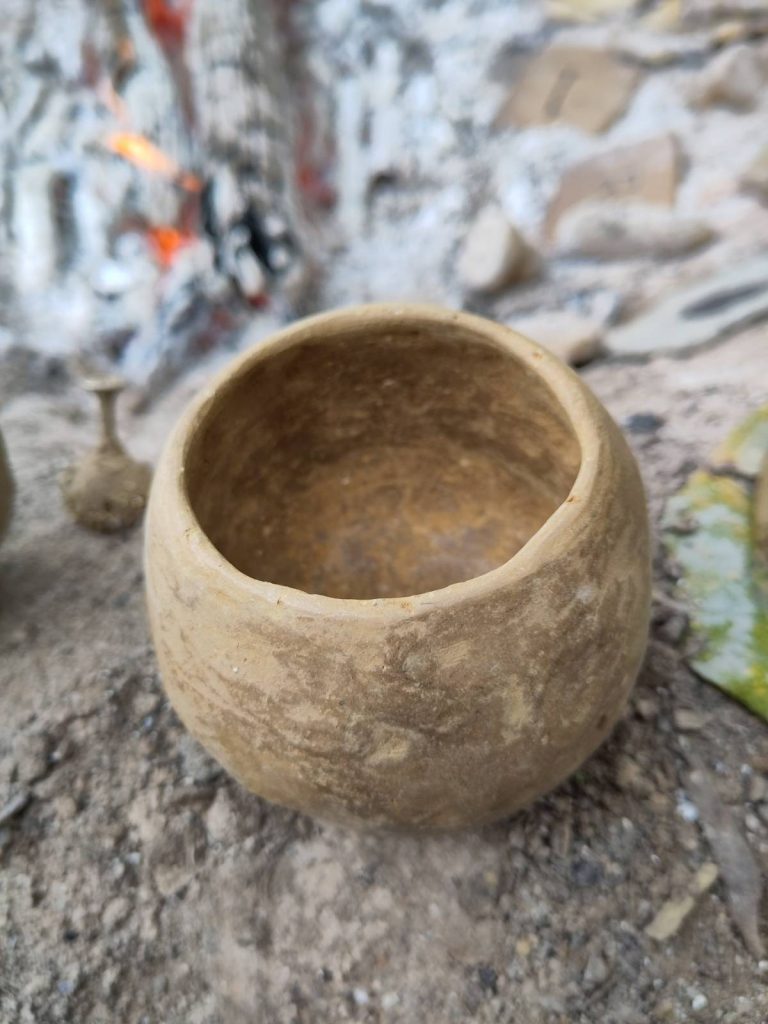
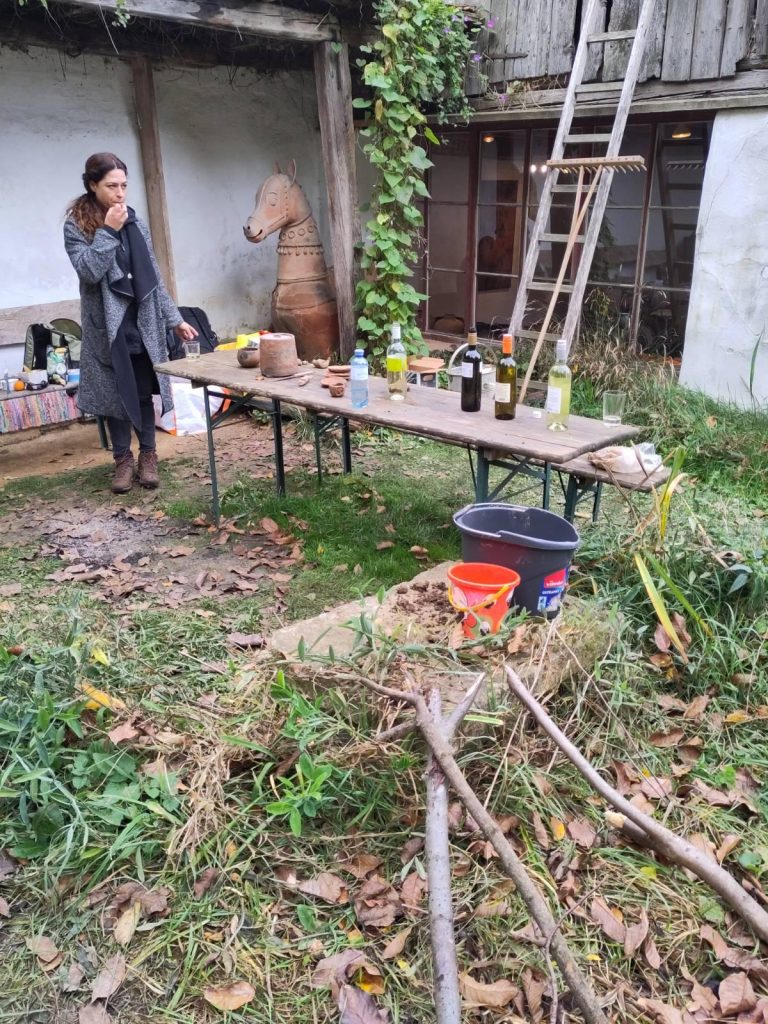
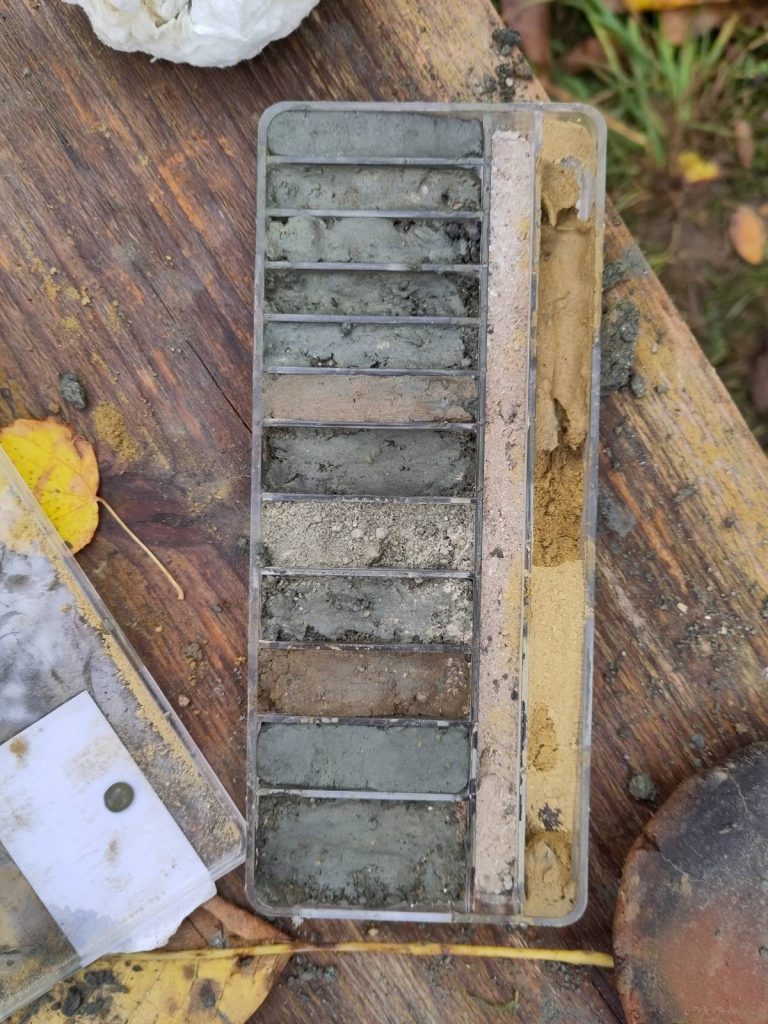
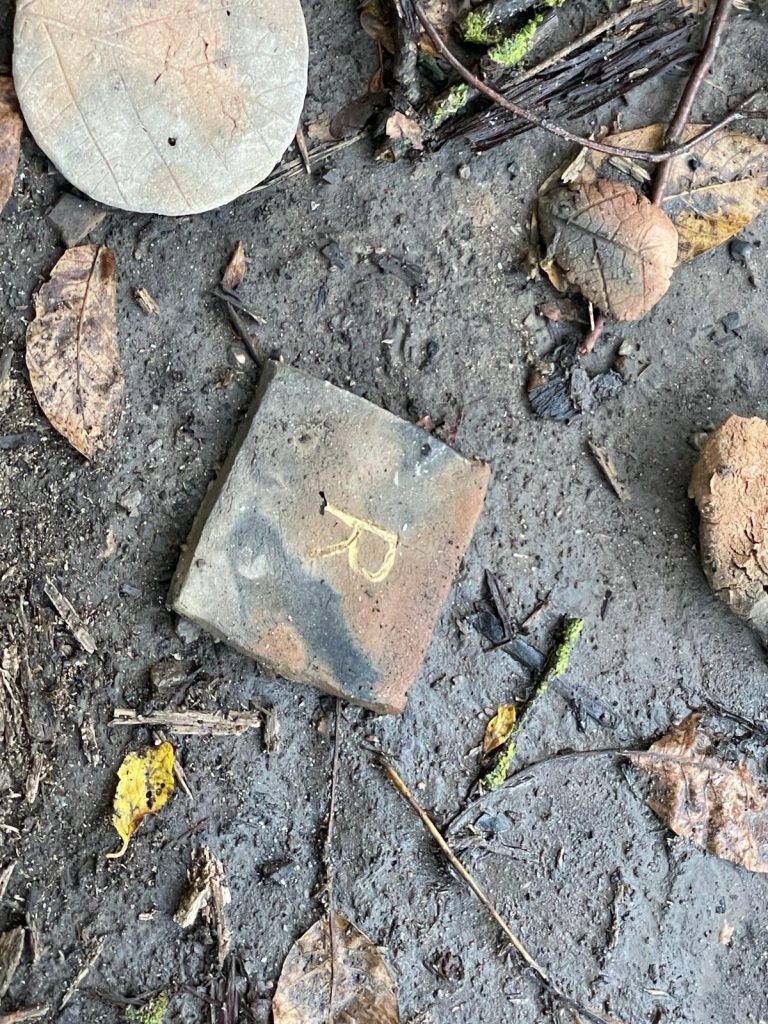